Shenyang gas filling block Five processes of product manufacturing:
1、 Aerator block The raw materials for storage and feeding are transported into the plant by truck, and the fly ash (or sand, stone powder) is gathered in the raw material yard and transported into the hopper when used. Bagged cement or bulk cement shall be stored in cement silo. When in use, it is loaded into the hopper. Chemicals, aluminum powder, etc. shall be stored separately in the chemical warehouse and aluminum powder warehouse, and transported separately to the production workshop during operation.
2. For the raw materials of aerated blocks, the ball mill is used to treat the fly ash (or sand and stone powder), which is sent to the ball mill through the electromagnetic vibration feeder and belt conveyor. The pulverized fly ash (or sand and stone powder) is separately sent to the slurry tank for storage by the fly ash pump.
Lime is sent to jaw crusher through electromagnetic vibration feeder and belt conveyor for crushing. The crushed lime is sent to lime storage bin through bucket elevator, and then sent to ball mill through screw conveyor. The ground materials are sent to powder batching bin through screw conveyor and bucket elevator. This shows that the production of raw materials is very important.
The chemicals are manually measured in a certain proportion to make a solution of a certain concentration and sent to the storage tank for storage.
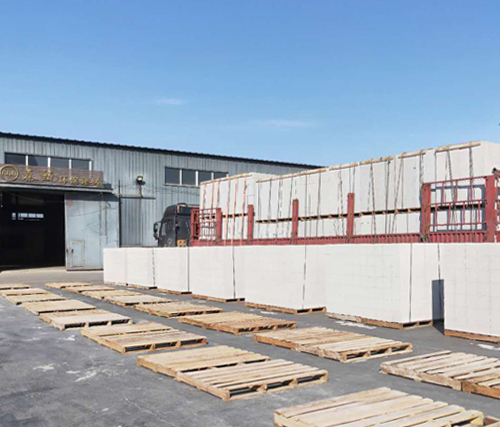
The aluminum powder is transported from the aluminum powder warehouse to the production workshop, lifted to the second floor of the batching building with an electric hoist, poured into the mixer for quantitative water addition, and stirred into an aluminum powder suspension 3. The aerated block batching, mixing, pouring lime, and cement are successively sent to the automatic metering scale for cumulative measurement by the screw conveyor under the powder batching bin. The screw conveyor under the scale can evenly participate in the pouring mixer.
Fly ash (or sand, stone powder) and waste slurry are put into the metering tank for metering. When the mold is in place after various materials are metered, slurry mixing can be carried out. The slurry should meet the process requirements (about 45 ℃) before pouring. If the temperature is not good, steam can be heated in the slurry metering tank, and aluminum powder suspension can be added 0.5~1 minute before pouring.
4. After the initial curing and cutting pouring of the aerated block, the mold is pushed into the initial curing room with the conveyor chain for initial gas generation and solidification. The room temperature is 48~68 ℃, and the initial curing time is 1.5-2 hours (according to the favorable geographical conditions, this process can be avoided). After the initial curing, the mold frame and the body are lifted to the cutting table where the bottom plate is placed in advance with the negative pressure lifting appliance. Remove the mold frame. The body is cut transversely, longitudinally Milling the head covering, lifting the mold frame back to the mold carrier for manual sorting and degreasing, and then lifting it to the mold carrier for mold assembly for the next pouring. The cut green body and the bottom plate of the kettle are lifted to the kettle carrier for stacking two layers with four supports between the layers, and several kettle carriers are grouped into one group.
The corner waste of the green body generated during cutting is sent to the waste slurry stirrer beside the cutting machine by the screw conveyor, and water is added to make waste slurry, which is to be used during batching.
5. After the autoclave of aerating blocks and the formation of product bodies on the parking line in front of the autoclave are completed, open the autoclave door to be discharged, pull out the product autoclave car inside the autoclave with a winch, and then pull the autoclave car to be autoclaved into the autoclave with a winch for curing. The products on the kettle car are lifted to the product warehouse with an overhead crane, and then transported to the product storage yard with a fork lift truck. The empty kettle car and kettle bottom plate are lifted back to the return line, and after sorting, they are pulled back to the stacking rack with a winch for the next cycle.
The content of this article comes from the network. If you have any questions, please contact us!