After long-term exploration of lightweight concrete production and summing up practical experience and lessons, if you want to mix high-quality Autoclaved aerated concrete Sand aerated block , the following points need to be checked at the same time:
1 Select appropriate mixing equipment
Most of the mixing equipment for lightweight concrete on the market use horizontal mixers, which are divided into single shaft mixers and double shaft horizontal mixers. The single horizontal shaft mixer is stable in mixing, and the foam is not easy to break, but the mixing speed is slow and the mixing efficiency is low; The double horizontal shaft mixer has fast mixing speed and high mixing efficiency, but the mixing is relatively intense and the foam damage rate is high. The two types of mixing host have their own characteristics. Considering the production efficiency, we choose a double horizontal shaft mixing host. In order to minimize the damage to the foam, it is necessary to select a suitable mixing speed for the double horizontal shaft mixing, and configure a frequency converter to convert the mixing speed of the equipment. After practical verification, when the mixing speed of the host is about 25r/min, Satisfactory concrete can be mixed.
2 Internal structure of mixer
In the actual production of lightweight concrete, the cementitious materials are mixed with water in the early stage. The materials in this mixing stage are delicate, viscous, cohesive, and difficult to disperse; Then add foam to mix lightweight concrete. At the moment of adding foam, it is difficult to mix it with viscous cement paste because of its low density and strong buoyancy. Therefore, the mixer is required to force mixing action.
The internal structure of the mixer for producing lightweight concrete should be different from that of the ordinary concrete mixer. The position and angle of the mixing arm need to be reasonably arranged to make the mixing force focus on mixing and give consideration to cutting, which not only makes the cement slurry and foam mix evenly, but also reduces the cement slurry block and slurry mass. In terms of mixing efficiency and strengthening the mixing effect, Double horizontal shaft mixer has advantages.
At the same time, in order to avoid the problem of material sticking in the internal structure of the mixer, the gap between the mixing arm and the mixing drum should be as small as possible. The bucket door should be designed at the lowest part of the mixing drum, and the size should be moderate. Because the fluidity of lightweight concrete is good, too small the bucket door will leave more dead corners, and too large the bucket door needs to work hard on the sealing of the bucket door.
3 Material sequence
Through actual production, we also found that the order of adding materials also has a great impact on the mixing effect. If cement is added first, or water and cement are added at the same time, it is easy to produce caking, slurry lumps or slurry lumps, because cement and other cementitious materials in the semi dry state are more likely to stick to the mixing drum or mixing arm, Therefore, it is difficult to mix it evenly again, and the uniformity of the cement slurry itself will become worse, thus affecting the next step of lightweight concrete mixing production. According to the on-site mixing experience, a certain amount of clean water is added according to the mixing ratio, followed by cement, fly ash additives, etc., and foamed foam is added after the mixing is uniform, so that caking is not easy to occur, and the foam and slurry are mixed quickly, and the mixing efficiency is also high.
Additional precautions:
1. Before using the mortar mixer, it must be accepted by the construction safety management department. After confirming that the mortar mixer meets the requirements, it is issued with a permit or has an acceptance Aerated concrete block The equipment can only be used after formalities. The equipment shall be hung with a certificate of conformity. The installation place shall be flat and solid, and the mechanical installation shall be stable and firm.
2. Temporary construction power shall be connected to neutral for protection, equipped with leakage protector, and equipped with three-level power distribution and bipolar protection. Generally, the mixer rotates in one direction for mixing. Therefore, when connecting to the power supply, attention should be paid to the direction of the arrow on the mixing drum.
3. Before starting the machine, check whether the insulation and grounding of electrical equipment are in good condition (such as protective grounding), and whether the protective cover of belt pulley is complete.
4. After startup, the mixing blade shall be idling first to check that the rotation direction of the mixing blade is correct, and then the mixing operation can be carried out while adding materials and water.
5. When the mortar mixer is feeding, it is not allowed to step on or use a spade or stick to pull down and scrape the mixing drum mouth. Tools cannot collide with the mixing blade, and it is not allowed to extend the tools into the hopper to scrape the slurry when rotating. No one is allowed to stand under the hopper of the mixer, and the safety hook must be hung when the hopper is lifted and stopped.
6. During operation, it is not allowed to put hands or sticks into the mixing drum or clean the mortar at the drum mouth.
7. In case of failure during operation, the power supply shall be cut off, and the mortar in the cylinder shall be poured out for maintenance and troubleshooting.
8. After operation, clean and maintain the mortar mixer inside and outside and clean the site, cut off the power supply and lock the box door.
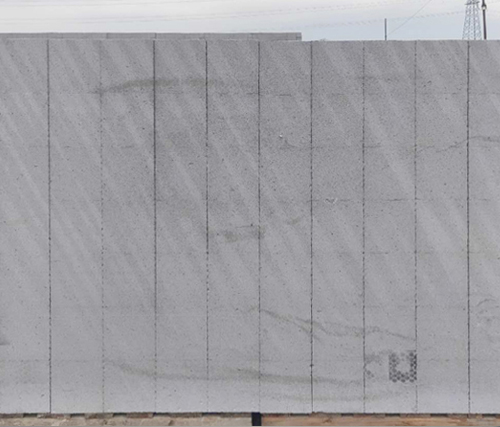