Talk about it Sand aerated block Required raw materials
1. Sand:
Sand is the core material of this product. Requirements: no impurities (bark, grass root, etc.), calcium carbonate (coral, shell, etc.) less than 10%. It shall comply with the specification (JC/T622-1996).
2. Cement:
Cement is the primary source of the initial setting strength of sand aerated concrete. It provides the primary calcium material for aerated concrete. The cement suitable for producing sand aerated concrete should be selected primarily from two aspects: the type and grade of cement. In production, 52.5 grade ordinary Portland cement should be selected first. In general, in order to reduce production costs, it is better to select 42.5 grade ordinary Portland cement.
3. Lime:
Lime is also one of the primary materials for the production of sand aerated concrete. Its primary role is to supply effective calcium oxide with cement, so that it can act with SiO2 and Al2O3 in siliceous materials under hydrothermal conditions to produce hydrated calcium silicate. Therefore, lime is one of the primary strength sources of this product. The effective calcium oxide content of lime used to produce aerated concrete should be more than 65%, and it is recommended that it should be more than 80%. It shall comply with the specification (JC/T621-1996).
4. Gypsum:
Gypsum in sand aerated concrete is the regulator of air generation process. The regulating effect of gypsum is mainly reflected in the delay of lime digestion and slurry thickening speed. The primary chemical component of gypsum is CaSO4. At present, there are three kinds of gypsum on the market: raw gypsum, anhydrite and plaster of paris. In addition, waste gypsum also occurs in the process of chemical production. Such as phosphogypsum discharged from phosphate fertilizer production, fluorogypsum discharged from fluorine chemicals production, titanium dioxide gypsum discharged from titanium dioxide production, etc. These gypsum have low cost and can replace natural gypsum to reduce production cost.
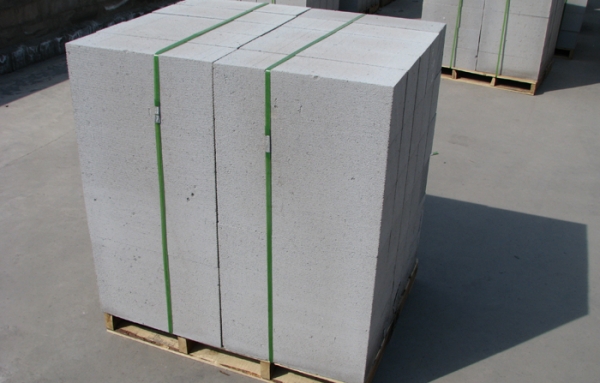
5. Gas generating agent:
In order to form lightweight porous structure, sand aerated concrete must have air evolution data as air evolution agent to make concrete have air holes.
6. Foam stabilizing agent:
After the air entraining agent is aerated, because the foam wall is relatively thin, under various conditions of disturbance, it sometimes simply breaks to defoamer, affecting the quality of concrete. Therefore, it is necessary to add foam stabilizer to the slurry. Our company is a manufacturer of sand aerated blocks with high cost performance. Welcome friends who need to negotiate and cooperate.
The content of this article comes from the network. If you have any questions, please contact me to delete it!